DC solid state relay and DC contactor, which one is better?
DC Solid State Relays (DC SSR) and DC contactors are both switching devices used to control circuits, but they have significant differences in working principles, performance and application scenarios:
-
Working Principle:
- DC Solid State Relay (DC SSR): Uses semiconductor devices (such as thyristors, transistors, MOSFETs or IGBT) to achieve circuit switching. It has no mechanical moving parts.
- DC Contactor: Controls the circuit by driving mechanical contacts to open or close through an electromagnetic coil.
-
Performance:
- DC SSR:
- No Mechanical Wear: Due to the absence of mechanical parts, DC SSRs generally have a longer lifespan.
- Fast Response: Capable of switching circuits within milliseconds.
- Noise-Free: Operates silently as there is no mechanical action.
- Low Power Consumption: Requires less power for the control circuit.
- DC Contactor:
- Mechanical Wear: The lifespan may be limited by the wear of contacts due to mechanical movement.
- Slower Response: Compared to SSRs, contactors have a slower response time.
- Noise: Produces mechanical noise when switching.
- Higher Power Consumption: The electromagnetic coil requires more power to maintain contact closure.
- DC SSR:
-
Application Scenarios:
- DC SSR: Suitable for situations requiring fast switching, noise-free operation, and high-frequency switching, such as precision electronic equipment and automation control systems.
- DC Contactor: Suitable for handling high current and high voltage situations, such as electric vehicles and industrial motor control.
-
Cost:
- DC SSR: Generally more expensive than DC contactors, especially in high-current applications.
- DC Contactor: Typically lower cost, suitable for budget-constrained applications.
In summary, the choice between these devices depends on specific application requirements, including current and voltage demands, switching frequency, noise sensitivity, and budget considerations.

Advantages of Low Voltage Drop DC Solid-State Relays - Heatsink is not required
Low voltage drop DC solid-state relays offer significant advantages in terms of efficiency, low heat generation, and high reliability, making them particularly suitable for applications requiring high efficiency and low energy consumption.
Read More
Mini Puck Solid-State Relay: A Compact and Reliable High-Efficiency Switching Solution
The GF1 solid state relay uses back-to-back thyristors for switching, which are more durable than traditional triacs.
Read More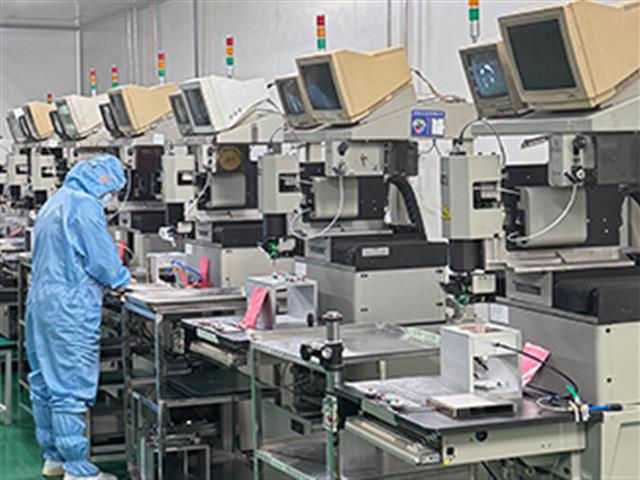
Difference Between Stud-Type and Capsule-Type Phase-Controlled Thyristors (PCT)
Capsule-type is better suited for higher power and more demanding heat dissipation requirements, while Stud-type is more appropriate for medium power applications with simpler installation needs.
Read More
Gas-Filled Relays vs. Vacuum Relays: A Comparison and Application in High Voltage Switching Technology
the difference between gas filled relay and vacuum relay
Read More