Advantages of Low Voltage Drop DC Solid-State Relays - Heatsink is not required
The main advantage of a low voltage drop DC solid-state relay is its lower energy loss during operation. Here are the specific benefits of low voltage drop:
1. Reduced Energy Loss
A low voltage drop means less voltage is lost when the relay is in the conducting state, thereby reducing power loss (Power Loss = Current × Voltage Drop). This is especially important in high-current applications, where a smaller voltage drop can significantly reduce heat generation and energy waste.
2. Improved Efficiency
In DC circuits, a low voltage drop improves the overall system efficiency, which is particularly critical in battery-powered or solar-powered systems.
3. Less Heat Generation
A low voltage drop results in less heat being generated within the relay, reducing the need for heat dissipation. This not only extends the relay's lifespan but also minimizes the need for additional cooling equipment.
4. Better Suitability for High-Current Applications
In high-current scenarios, a low voltage drop solid-state relay can handle large currents more effectively without causing excessive energy loss or overheating.
5. Enhanced System Stability
A low voltage drop reduces voltage fluctuations in the circuit, thereby improving system stability and reliability.
6. Ideal for Low-Voltage Systems
In low-voltage DC systems (e.g., 12V or 24V systems), every volt of voltage drop can significantly impact system performance. A low voltage drop relay minimizes this impact.
In summary, low voltage drop DC solid-state relays offer significant advantages in terms of efficiency, low heat generation, and high reliability, making them particularly suitable for applications requiring high efficiency and low energy consumption.
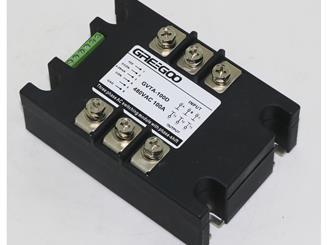
What's the difference between phase control Thyristor Module and Rectifier Diode Module?
Thyristor modules are used for controlled switching and power regulation, while rectifier diode modules are employed for converting AC to DC in rectification applications.
Read More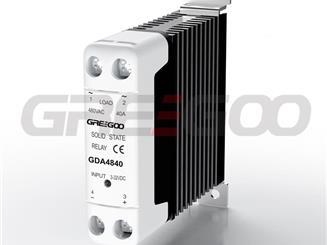
How to choose a suitable Solid State Relays
Single phase or three phase, nominal voltage and current, potential surge or inrush current, AC or DC load, control signal, zero crossing type or random control ssr etc.
Read More
Fast Recovery Epitaxial Diode vs Fast Recovery Diode Module
Key Differences Fast Recovery Epitaxial Diode vs Fast Recovery Diode Module
Read More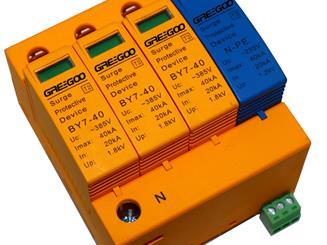
What are the main differences between MOVs and Spark Gaps in SPDs?
An effective surge protection strategy often combines the use of both MOVs and spark gaps, along with other protective devices, to provide comprehensive protection against different levels of power surges.
Read More