Thyristor Module
Home Products Thyristor Diode ModuleSemikron Thyristor Diode ModuleThyristor Module
Thyristor Module
The thyristor module is a type of power electronic device module, primarily used in control and rectification circuits. It consists of one or more thyristors (SCR, Silicon Controlled Rectifier) and is typically packaged in a module for easy installation and use. Below is some key information about thyristor modules:
Working Principle
A thyristor is a three-terminal semiconductor device with an anode, cathode, and gate. By applying a trigger signal to the gate, the thyristor's conduction and cutoff can be controlled. Thyristor modules are commonly used in high-voltage and high-current applications.
Main Applications
Rectification Circuits: Converting AC to DC.
Motor Control: For speed regulation and soft start.
Power Control: Such as power adjustment for heaters.
Inverters and Converters: Used in power electronic equipment.
Advantages
High voltage and high current handling capability.
High efficiency and low power consumption.
High reliability, suitable for industrial applications.
Common Types
Single Thyristor Module: Contains only one thyristor.
Dual Thyristor Module: Contains two thyristors, often used in AC circuits.
Three-Phase Thyristor Module: Used for rectification or control of three-phase power.
Selection Considerations
Voltage and Current Ratings: Choose a suitable module based on application requirements.
Trigger Circuit: Ensure the gate trigger signal's voltage and current meet the requirements.
Heat Dissipation: Thyristor modules generate heat during operation, so good thermal management is necessary.
The differences between single thyristor modules, dual thyristor modules, and three phase thyristor modules mainly lie in their structure, functionality, and application scenarios.
A single thyristor module contains only one thyristor and is suitable for unidirectional rectification or switching control in single-phase circuits. A dual thyristor module includes two thyristors connected in reverse parallel, enabling bidirectional control of AC power, commonly used in dimmers, motor speed controllers, and other AC voltage regulation applications. A three phase thyristor module contains three thyristors and is designed for three-phase circuits, suitable for rectification or power regulation, widely applied in industrial equipment such as three-phase motor control and three-phase rectifier power supplies.
In summary, single thyristor modules are ideal for simple single-phase rectification, dual thyristor modules for single-phase AC regulation, and three thyristor modules for complex three-phase circuit control. Choosing the appropriate module type based on specific application needs ensures more efficient circuit design.
Thyristor modules and diode modules can both be used to convert AC to DC, but they differ significantly in terms of working principles, control methods, and application scenarios. Below are their main differences:
Working Principle
Thyristor Module:
A thyristor is a controllable semiconductor device with an anode, cathode, and gate.
It requires a trigger signal at the gate to control its conduction and cutoff.
Thyristor modules enable controlled rectification, allowing adjustment of the output DC voltage.
Diode Module:
A diode is a unidirectional device with only an anode and cathode, without a control terminal.
Its conduction is determined solely by the voltage polarity in the circuit and cannot be controlled.
Diode modules provide uncontrolled rectification, where the output DC voltage is fixed and cannot be adjusted.
Control Capability
Thyristor Module:
Offers control capability, allowing adjustment of the conduction angle via the gate trigger signal to regulate the output voltage.
Suitable for applications requiring adjustable output voltage or power, such as motor speed control and heater power regulation.
Diode Module:
Cannot control conduction; the output voltage is entirely determined by the input voltage.
Suitable for applications where no adjustment is needed, such as simple rectification circuits.
Efficiency and Complexity
Thyristor Module:
Requires additional trigger circuits, making the system design more complex.
May have some power loss during partial conduction but offers flexible control.
Diode Module:
Simple structure with no need for additional control circuits, resulting in higher efficiency.
Ideal for applications with high demands for cost-effectiveness and efficiency.
Application Scenarios
Thyristor Module:
Used in scenarios requiring adjustable output voltage or power, such as:
Motor control (speed regulation, soft start).
Controlled rectification circuits.
Industrial heating equipment.
Diode Module:
Used in simple rectification scenarios, such as:
Power supply rectification (AC to DC).
DC power supply equipment without adjustment requirements.
Summary
Choose a thyristor module if adjustable output voltage or power is needed.
Choose a diode module if only simple rectification is required.
The dual thyristor module's in series, common cathode, and common anode circuits differ in connection methods and application scenarios:
In Series Circuit: The anode and cathode of two thyristors are connected in series, suitable for high-voltage scenarios by sharing the voltage. Each thyristor requires an independent trigger signal to ensure synchronous conduction. It is commonly used in high-voltage direct current (HVDC) transmission and high-voltage power control.
Common Cathode Circuit: The cathodes of two thyristors are connected together, sharing a common cathode terminal. It is suitable for dual independent control of forward currents. The trigger circuit design is relatively simple and is often used in dual-output rectifier circuits and multi-load independent control scenarios.
Common Anode Circuit: The anodes of two thyristors are connected together, sharing a common anode terminal. It is suitable for dual independent control of reverse currents. The trigger circuit needs to consider the independence of the cathodes and is often used in reverse current control and specific AC regulation scenarios.
In summary, series circuits are used for high-voltage control, while common cathode and common anode circuits are suitable for multi-path independent control of forward and reverse currents, respectively. The specific choice depends on application requirements.
Thyristor modules and thyristor bridges differ significantly in structure and function.
A thyristor module is a device that encapsulates one or more thyristors, primarily used for high-voltage or high-current switching control, suitable for simple circuit applications such as industrial heating or motor starting. A thyristor bridge, on the other hand, is a circuit topology composed of multiple thyristors, commonly used for power conversion, such as rectifiers, inverters, or frequency converters, and is ideal for complex power electronic equipment like motor drives and UPS systems.
In summary, a thyristor module is a single switching component, while a thyristor bridge is a circuit structure for AC-DC conversion, with the choice depending on specific application requirements.
The main difference between a thyristor bridge and a diode bridge lies in their control capabilities and application scenarios. A thyristor bridge is composed of thyristors, which are controllable and can adjust output voltage or current by regulating the firing angle. It is suitable for applications requiring power regulation, such as DC motor speed control and controlled rectifiers. A diode bridge, on the other hand, consists of ordinary diodes and is uncontrollable, used solely for converting AC to DC, commonly found in simple rectifier circuits like power adapters. The thyristor bridge is more complex and costly but offers greater functionality, while the diode bridge is simpler and cheaper but has limited functionality. The choice depends on specific needs: for adjustable output, choose a thyristor bridge; for basic rectification, choose a diode bridge.
Need more information?
Contact us to request pricing, availability and customization options.

SKKT series thyristor modules
SKKT 15 to 570A thyristor modules, semikron thyristor module
View More
Antiparallel Thyristor Modules SK25KQ
SK25KQ single phase
View More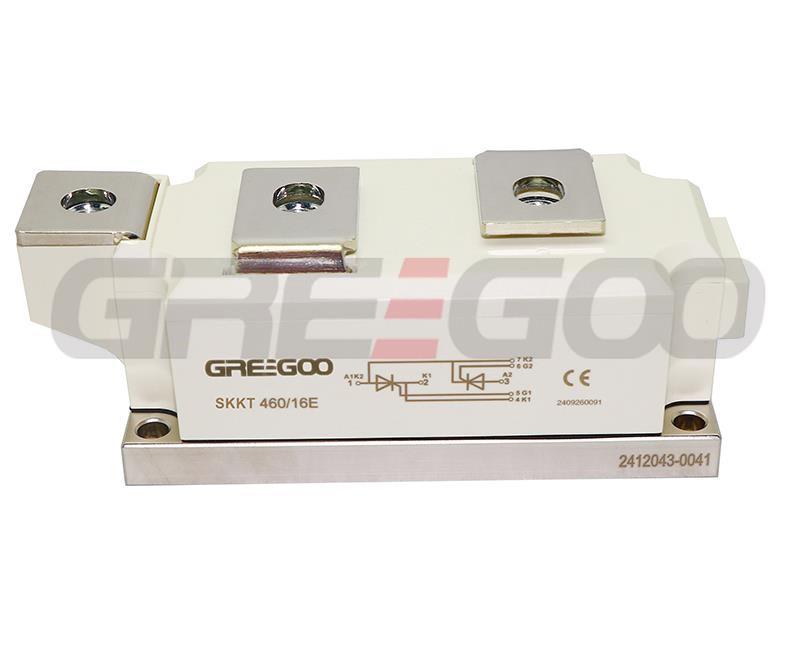
SKKT460 SKKH460 Thyristor Diode Module
460A 1600V Dual Thyristor Module and Thyristor Diode Module
View More
SKKT 273/16E Thyristor Modules
SKKT273, SKKH273
View More